Nonconformance Management
Elevate Product and Service Quality
With Nonconformance Management Software organizations gain insights into the root causes of nonconformities. This understanding enables targeted interventions, preventing recurrence and elevating overall product and service quality. By addressing issues at their core, organizations can deliver offerings that meet and exceed customer expectations.
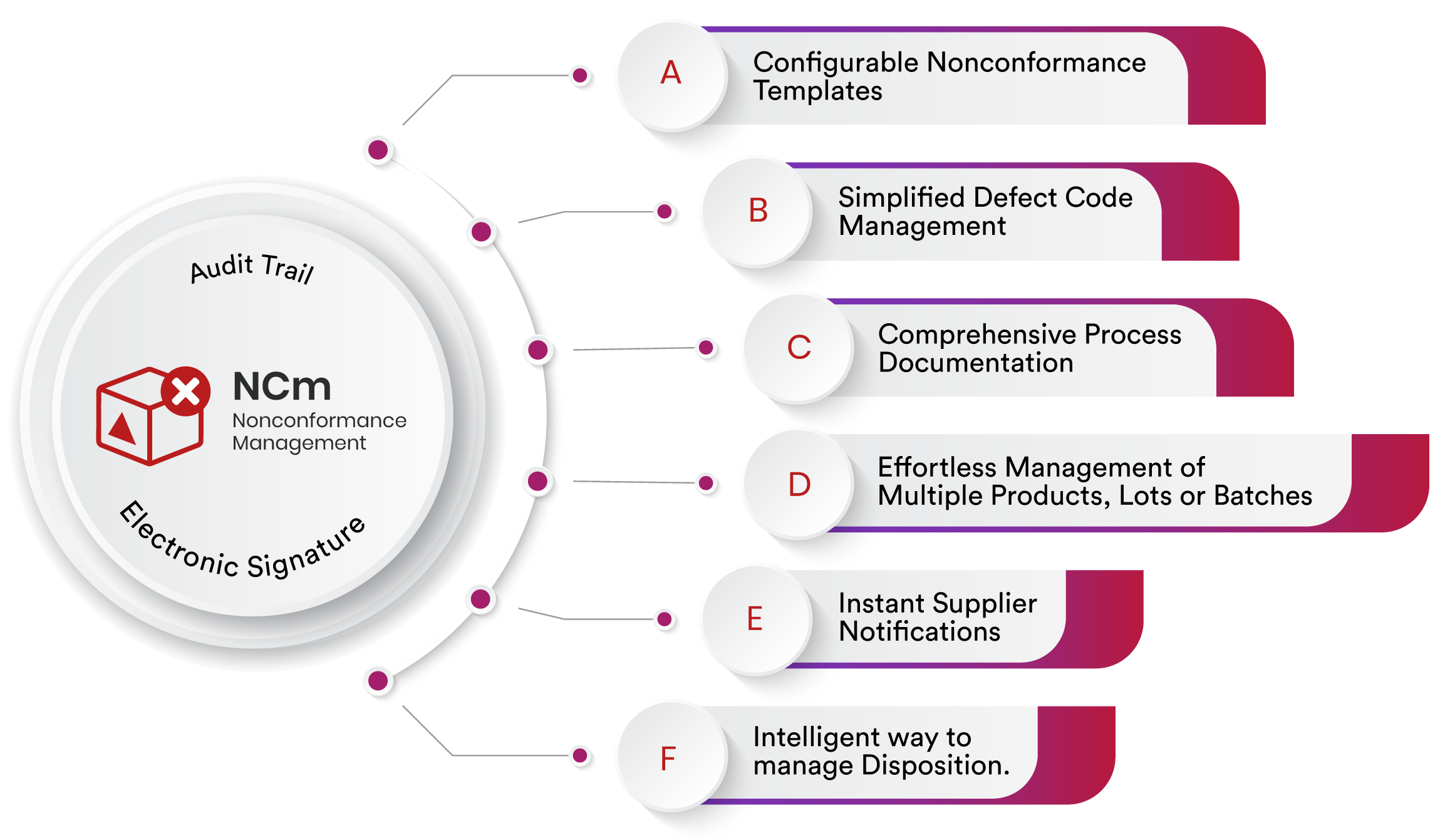
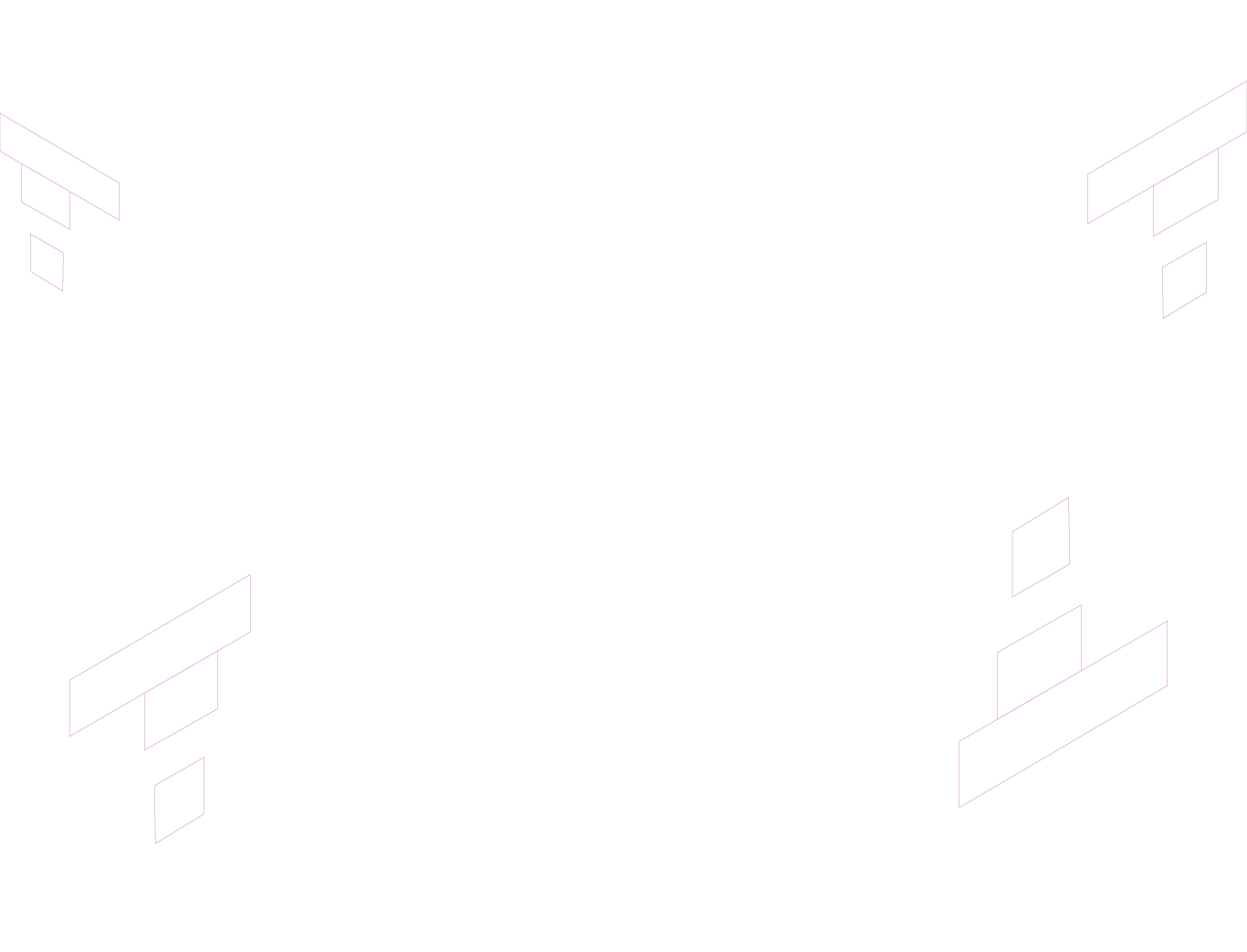
Elevating Nonconformance Management with Embedded AI
Qualityze Nonconformance Management Software empowers organizations to seamlessly automate the entire nonconformity lifecycle. From identification to resolution, each step is streamlined, leading to a substantial reduction in errors and response times. This pivotal enhancement translates into improved operational efficiency, ultimately driving the organization towards achieving operational excellence.

Configurable Nonconformance Templates
A harmonized approach to nonconformance management is essential. Qualityze solution presents configurable templates that serve as a blueprint for standardizing NC workflows, approvals, and custom fields. By applying consistent configurations, organizations ensure efficiency and adherence to established protocols, laying the foundation for defined NC management.

Simplified Defect Code Management
Qualityze Nonconformance management software understands the pivotal role defect codes play in the categorization process. To enhance this critical function, Qualityze has developed a streamlined defect code management feature that simplifies every step. When a new defect code is identified, our system offers an effortless "New" option for its addition. This user-friendly process ensures that no potential nonconformance category is overlooked. For frequently occurring nonconformities, our system offers a dropdown menu of existing codes. This smart selection mechanism ensures consistency and standardization in categorization. Users can quickly and accurately choose the appropriate defect code, aligning with established categorization practices.

Comprehensive Process Documentation
In-depth understanding is the cornerstone of effective nonconformance management. Qualityze system facilitates the capture of every relevant detail contributing to the NC workflow. This includes process specifics, defects, codes, root causes, manufacturing and supplier information, as well as customer details. This centralized repository optimizes NC resolution by providing a holistic perspective.

Effortless Management of Multiple Products, Lots or Batches
Managing Nonconformances involving multiple products, lots or batches is simplified through Qualityze platform. Additional products can be added without complication. Users provide relevant details such as manufacturing sites, lot numbers, units of measurement for each batch number. This precision ensures accurate representation of quantities, enhancing the accuracy of NC data.

Instant Supplier Notifications
When a nonconformance incident occurs, time is of the essence. Effective collaboration with external stakeholders is paramount for swift issue resolution. Qualityze offers a supplier notification feature, enabling users to promptly inform suppliers about specific nonconformance incidents. The supplier notification feature is more than just a messaging tool. It's a conduit for efficient engagement to streamline communication, with the added capability to attach supporting documentation, ensuring clear and efficient supplier engagement.

Intelligent way to manage Disposition.
Qualityze Nonconformance management software introduces an advanced and meticulous disposition task, seamlessly infused with embedded artificial intelligence (AI). This groundbreaking approach ensures the accurate linkage of intricate data points, including product specifics, lot numbers, defect quantities, and the precise disposition codes. Moreover, AI-driven intelligence continues to vigilantly track the progress of disposed defect quantities, confirming that every nonconformance is effectively resolved. This multifaceted approach empowers organizations to navigate the complexities of nonconformance seamlessly, resulting in elevated quality management and a resolute drive towards operational excellence.
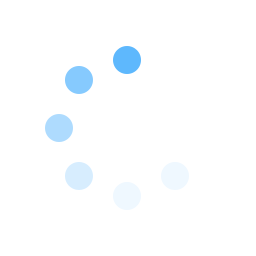
Loading random fact...
COQ
The cost of quality is largely driven by Prevention Costs, Appraisal Costs, Internal Failure Costs, and External Failure Costs. Qualityze NonConformance Management Software enables organizations to track and analyze nonconformance trends, helping identify root causes and implement corrective actions to prevent recurrence.
- Identifies and addresses nonconformances at an early stage to reduce the Cost of Quality.
- Tracks and analyzes nonconformance trends to identify root causes and implement corrective actions.
- Minimizes costs associated with rework, scrap, and customer complaints.
- Streamlines nonconformance resolution processes, saving time and effort.
- Promotes a culture of continuous improvement to optimize quality.
- Reduces the overall Cost of Quality in the organization.
Nonconformance management benefits to various operational functions
Every business function has unique expectations from a solution, find out what Qualityze can deliver from your functions perspective.
Quality Assurance
Nonconformance management system helps in identifying and addressing quality issues, ensuring that products or services meet the required quality standards.
Production and Manufacturing
By effectively managing nonconformances, production and manufacturing processes can be optimized, reducing defects and improving overall product quality.
Supply Chain Management
Nonconformance management system allows for better management of supplier quality, ensuring that noncompliant products or materials are detected and addressed before they enter the supply chain.
Compliance and Regulatory Affairs
Nonconformance management system helps organizations ensure compliance with industry regulations and standards, avoiding potential penalties or legal issues.
Continuous Improvement
Through the analysis of nonconformances, organizations can identify areas for improvement and implement corrective actions to prevent similar issues in the future, driving continuous improvement initiatives.
Customer Satisfaction
By effectively managing nonconformances, organizations can enhance customer satisfaction by delivering products or services that meet or exceed customer expectations.
Experience Qualityze Difference in managing Quality
We empower organizations to uphold exceptional quality standards while providing the following advantages:
Configurable Cloud-Based Platform
Our system is developed on the world's foremost cloud-based platform, Salesforce.com, which allows businesses to effortlessly personalize it to their exact requirements. It is an adaptable and scalable system that expands in tandem with the growth of your organization. Its wide-ranging configurability broadens the functional scope of an EQMS to an infinite array of creative applications, making it an extremely valuable solution for your organization.
Compliance Ready
Our system adheres to compliance standards for every industry and follows the relevant regulations set by regulatory committees, such as the Food and Drug Administration (FDA) - 21 CFR Part 820, International Organization for Standardization (ISO) - ISO 9001, ISO 13485, Pharmaceuticals and Medical Devices Agency (PMDA), Therapeutic Goods Administration (TGA), China Food and Drug Administration (CFDA), and others.
User-Friendly Interface
Our system design makes it easy for users to accomplish their goals and complete tasks, while minimizing errors and confusion. It considers the needs of various user groups, and provides clear and helpful feedback throughout the user journey. Qualityze strives to create an emotional connection with the user, resulting in increased satisfaction, loyalty, and a positive brand image.
The Start of Something Amazing.
Request Demo
Frequently asked questions
Answers to commonly asked questions
If you have more questions feel free to reachout to us.
Contact UsGeneral
- Contact Qualityze: You can contact Qualityze through their website, email, or phone to get more information about their EQMS solutions and to schedule a demo.
- Demo: Qualityze will provide you with a demo of their EQMS solutions, which will help you to understand how the system works and how it can be customized to meet your specific needs.
- Requirement gathering: Once you have decided to move forward with Qualityze, you will work with their team to gather your requirements, including any specific standards you need to comply with.
- Configuration: Qualityze will then configure the system to meet your specific requirements, including setting up workflows, forms, and reports.
- User training: Qualityze will provide user training to ensure that your team is familiar with the system and knows how to use it effectively.
- Go-live: Once the system is configured and your team is trained, you can go-live and start using Qualityze EQMS to manage your quality processes, including NonConformances.
How Qualityze can help me in managing NonConformances?
Qualityze provides a comprehensive Nonconformance Management solution that helps you manage the entire nonconformance process efficiently. The solution streamlines the process of identifying and reporting nonconformance events, tracking the investigation process, and managing the corrective and preventive action (CAPA) plans to prevent similar issues from occurring in the future.
With Qualityze Nonconformance Management software, you can easily comply with industry-specific standards like ISO 9001, ISO 13485, 21 CFR Part 11, 21 CFR Part 820, AS9100, and IATF 16949, and ensure that best practices are followed. You can also configure workflows and approval processes to suit your organization's specific needs and get real-time insights into the status of all nonconformance events. This enables you to take prompt corrective actions, reduce the risk of noncompliance, and improve product quality while ensuring customer satisfaction.
How quickly Qualityze EQMS can be deployed in my organization?
Qualityze EQMS can be deployed in your organization in a matter of weeks, depending on the size and complexity of your organization's requirements. Our experienced implementation team follows a well-defined and proven process to ensure a smooth and seamless deployment of the system. We also provide comprehensive training and support to help your team get up to speed with the system quickly.
How can I start using Qualityze EQMS?
To start using Qualityze EQMS, you can follow these steps:
Compliance
How Qualityze EQMS ensures compliance?
Qualityze EQMS ensures compliance by providing features that comply with industry-specific standards, such as ISO 9001, ISO 13485, 21 CFR Part 11, 21 CFR Part 820, AS9100, and IATF 16949. The solution is built on the Salesforce platform, which provides a secure and compliant cloud infrastructure. Qualityze EQMS allows businesses to maintain a complete audit trail of all quality data, ensuring regulatory compliance and reducing the risk of non-compliance.
The software also provides configurable workflows that allow businesses to enforce compliance with their own internal policies and procedures. The workflows can be customized to fit specific requirements and ensure that all processes are standardized and consistent across the organization. The solution provides real-time visibility and reporting, allowing businesses to quickly identify areas of non-compliance and take corrective action. Qualityze EQMS also provides automatic version control and document management features, ensuring that all documents are up-to-date and comply with relevant regulations.
How Qualityze can provide free life time updates? What does “free lifetime update" include?
As a cloud-based solution, Qualityze EQMS is continually updated with the latest features and functionalities to ensure compliance with changing regulations and industry standards. Qualityze provides free lifetime updates to its customers to keep them up-to-date with the latest technology advancements and features. These updates are automatically applied to the system without any additional cost or disruption to the user. Qualityze’s software as a service (SaaS) model allows for seamless integration of new features and bug fixes, which means that customers always have access to the latest version of the software. Qualityze’s dedicated team of developers and quality experts continuously work on enhancing the product to ensure that it meets the evolving needs of the customers and helps them stay ahead of the competition.
What does Qualityze's free lifetime update include?
Qualityze's free lifetime updates include bug fixes, security updates, feature enhancements, and new functionalities. These updates ensure that the Qualityze EQMS solution stays up-to-date and continues to meet the evolving needs of the industry and regulatory standards. The updates are provided without any additional cost to the customers and are automatically deployed to their systems. The Qualityze team ensures that the updates are thoroughly tested before being released to the customers to ensure their smooth integration and minimal disruption to their business operations. The free lifetime updates help customers to leverage the latest technological advancements and ensure that their quality management processes remain compliant and effective.
Security
- Data Encryption: Qualityze uses AES-256 encryption to secure data in transit and at rest, providing a high level of data security.
- Role-Based Access Control: Qualityze provides access controls based on user roles, ensuring that users only have access to the data they need to do their job.
- Two-Factor Authentication: Qualityze uses two-factor authentication to provide an additional layer of security when logging in to the system.
- Regular Security Audits: Qualityze conducts regular security audits to identify and address any vulnerabilities in the system.
- Compliance with Industry Standards: Qualityze complies with industry-specific standards such as ISO 9001, ISO 13485, 21 CFR Part 11, 21 CFR Part 820, AS9100, and IATF 16949, ensuring that the system meets the highest security standards.
How secured is Qualityze EQMS?
Qualityze EQMS provides a highly secure environment for managing quality data. It is built on the world’s leading cloud-based platform, Salesforce.com, which has a robust security framework with multiple layers of security features, including:
Overall, Qualityze EQMS provides a secure environment for managing quality data, giving organizations peace of mind that their sensitive data is protected.