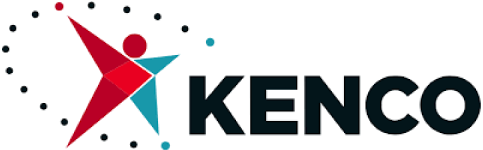
Qualityze Drives Innovation and Continuous Improvement with Strategic Partnership
We have a Strategic Partnership with Qualityze. They have been an incredible partner in the configuration and
implementation of the eQMS software. I have participated in several system implementations across multiple platforms and Qualityze is ...
Corporate Quality Assurance Manager, Kenco Group
Excellent support shifting audits to Salesforce
I-CAR is a training organization with hundreds of instructors around the country. We regularly evaluate our instructors to provide quality and relevant education to our students. Due to rapid growth over a few years, our home-built system became i...
Manager, Quality Engineering

Excellent Quality Management Solution
I manage training and document control. An effective document control system is among the most critical tools for
compliance in highly regulated industries like ours. Document control is essential in QA/RA environments because it
touches all...
Omron Healthcare, Inc

Qualityze For Our eQMS
With every new product comes the anxiety of, “Will this work? Is it complicated? Will I have support, etc.?” but with
Qualityze and their team, they not only met our needs, but they also surpassed our expectations. Qualityze has pro...
Ortho8
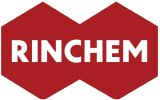
Qualityze: A powerful product to manage all your quality needs
Rinchem is focused on third party warehouse and transportation logistics. The growth in our company has lead to a need for a robust system that can manage multiple pillars of quality, from start to finish within the same system. We have implemente...
Application Analyst, Rinchem
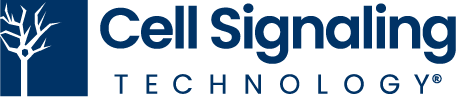
The right fit and great support
For years we had managed all our documents, training, and changes manually using numerous spreadsheets and multiple applications. As our business grew, continuing with those methods was not feasible. We spent many months reviewing many different o...
Sr. Manager, Quality Systems, Cell Signaling Technology
Qualityze Organized Our Quality Processes
Our business was growing rapidly, and we needed help to get us organized, that’s when brought in the Qualityze Team. The Qualityze Team helped us execute our vision for the company and organized our processes to industry best in class standa...
Administrator, Blue Rabbit
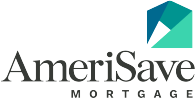
Qualityze Our EQMS Solution
As our company’s complaint volume increased, we decided that a new system would be needed to accurately track and report on our consumer complaints. After researching, we landed with Qualityze as our best EQMS vendor of choice. The Qualityze...
Sr. Compliance Analyst, AmeriSave Mortgage Corporation
We chose Qualityze for its simplicity!
Qualityze is an out-of-the-box, ready-to-use, Quality Management System. Since it runs as an independent, Cloud-based application, which is much nicer than trying to expand an expensive ERP system, muddied with a bunch of unwanted ERP features; th...
Quality Coordinator Master Tag Montague, MI

Qualityze EQMS implementation experience and features!!!
Our experience working with the Qualityze implementation and support team was extremely positive. They made sure we understood their base product and the best ways to fit the product to our business processes through configurations to enable ...
Global Quality Assurance Manager
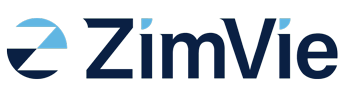
Qualityze eQMS with Incredible Customer Service!
Our business was faced with tight timelines to go live in a new electronic Quality Management System, and the Qualityze team made it happen! Our business has numerous complexities related to different sites operating under d...
Associate Supplier Quality Manager at ZimVie Spine
Our experience with Qualityze EQMS
From the moment we partnered with Qualityze Inc. for our Quality Management System needs, we knew we made the right choice. The system itself has transformed our quality management practices, providing us with the tools and insights we need to mai...
Daniel Boo
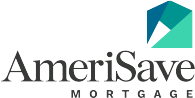
Qualityze our EQMS System
My team and I worked with Qualityze to implement a Complaint management solution which provided dashboards, reporting, response templates and the Documents module for policies and procedures. We completed much of the work at a very busy time. The ...
AVP of Compliance, AmeriSave Mortgage Corporation
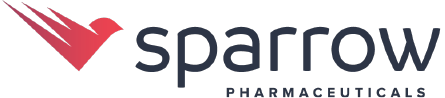
A great choice for an eQMS!
After months of reviewing potential Electronic QMS software packages for our company we concluded that Qualityze was the clear choice for us. The task of implementing this type of system seemed quite daunting but working with the team at Qualityze...
QA Consultant, Sparrow Pharmaceuticals
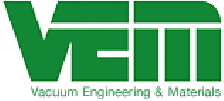
Qualityze has been instrumental Partner for our QMS system
Qualityze has been instrumental in our companies transition from ISO 9001 to IATF 16949. Auditor from our registrar and customers have been impressed by the use of the Qualityze modules. The Qualityze team is easy to work with, and helpful in find...
Vacuum Engineering and Materials
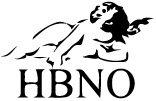
Our Experience with Qualityze Implementation.
HBNO CO. is a relativity new company, started 7 years ago, and growing bigger year after year. In 2021, our management thought of introducing an EQMS system which could automate our existing process and move us away from a paper-based process to a...
Industrial Engineer IL, Health & Beauty Natural Oils Co., Inc
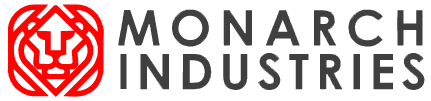
Qualityze Implementation For Fast-Paced Manufacturing
We are a rapidly growing manufacturing organization that seeks to integrate our quality system software with various other programs, including our MRP system. After months of searching the right solution and fit, we determined that the Qualityze Q...
Director of Quality Operations, Monarch Industries Limited

Qualityze has met all of our requirements.
Infinity Molding and Assembly is a small custom injection molder that was using a highly paper based QMS. The search began for a new QMS software and after months of searching and previewing a few other systems we chose to more forward with Qualit...
Quality Systems Manager, Infinity Molding & Assembly
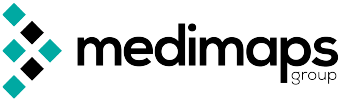
Our experience with Qualityze eQMS
Over the past year Medimaps has implemented six of the Qualityze QMS modules to migrate the most relevant parts of the company’s Quality Management System to an electronic tool. The Qualityze team has been remarkable in competence and effici...
Director of Regulatory and Quality, Medimaps Group SA
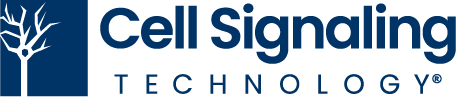
Methodical and collaborative experience!
With a small Quality Team, the implementation of Qualityze allowed us to notice drastic improvements in our workflows. Working with Qualityze has been great, and that has clearly been demonstrated with the easy transition and ease of product usage...
Quality Specialist, Cell Signaling Technology
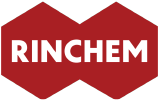
Best Business Partner for QMS
Over the past year Rinchem has implemented several the Qualityze QMS modules to enhance our Quality department. Our Qualityze team has been excellent partners in development and customizations to meet our specific requirements. They have provided ...
QMS Document Control Coordinator, Rinchem Co. Inc.

Highly Recommend
Our company has been growing rapidly & we absolutely needed an eQMS solution immediately. Qualityze’s capabilities surpassed our wish list & the modules met our requirements. Implementation has been an ideal transition with guided as...
Chief Regulatory Office, Ortho8

Excellent Quality Management System
Qualityze has made our processes much more organized. Everything is in one place, and it is easy to search and run
reports. The Qualityze team has also been extremely helpful as we implement new modules and help find ways to improve processes t...
QA Analyst, Omron Healthcare, Inc
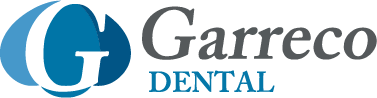
Excellent software for document management and QA tasks
In the past, our medical device company struggled to efficiently manage Quality processes such as document management, non-conformances, audits, employee trainings, customer complaints and CAPAs. After a systematic search and assessing multiple QM...
Quality Director, Garreco Dental

Incredible Value, Incredible Partner
Qualityze drives value through innovation and they are quite dedicated to this. The differentiator for Qualityze is
their outstanding commitment to customer service and innovation. We could not ask for a better partner and it doesn’t hurt...
Director, Quality Assurance & Regulatory Affairs, Kenco Group
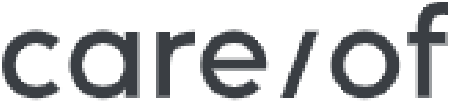
Amazing Cloud EQMS Software!!!!
After looking, viewing demos from several Quality Management Solutions, Qualityze checked off all the boxes of being cloud-based, user-friendly, and totally customizable. The Qualityze team has been very supportive and helped us every step of the ...
Sr. Manager Quality, Care/Of
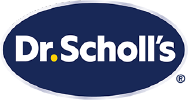
Exceeded Our Strategic Goals in an Exceptionally Efficient Manner. All QMS processes in one system!!
We currently have multiple solutions that resulted in us having disparate quality systems to manage with multiple operational challenges. We were looking for a solution that could consolidate all our quality systems into one centralize repository....
Quality Assurance Coordinator, Scholls Wellness
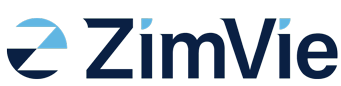
Qualityze - Enterprise Quality Management Solution (EQMS)
Our organization selected Qualityze as our new eQMS system as our previous eQMS process includes the use of multiple systems across the business and associated costs for each. Qualityze provided us with a solution as a system that is highly c...
ZimVie Quality Director
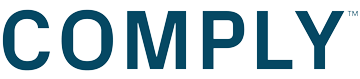
Qualityze EQMS Implementation Experience
My team and I were looking for an audit management system to accommodate a unique audit workflow. Working very closely with the Qualityze technical team, I can honestly say that they were always patient and provided me with clear guidance on how t...
SVP, Advisory Consulting COMPLY
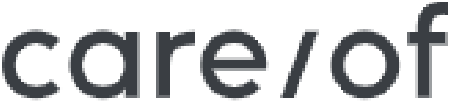
Thank you Qualityze!
Qualityze has tremendously helped our business fit its complicated model into an electronic quality management system. It has wonderful reporting and dashboard capabilities, as well as being totally customizable to fit our business’s needs. ...
Quality Control Associate, Care/Of